解决自动上下料激光切管机加工厚碳钢小轮廓切割过烧的方法
解决加工12毫米厚25毫米见方形状时频繁发生过烧的方法
【现象】
切割碳钢材料时,如果加工形状中存在尖角,则很容易发生尖角部的熔损或过烧。切割速度会随着加工板厚的增加而下降,且切割中所产生的热量会不断在材料内积蓄,导致材料温度升高,使得尖角部熔损或过烧现象频繁发生。
【原因】
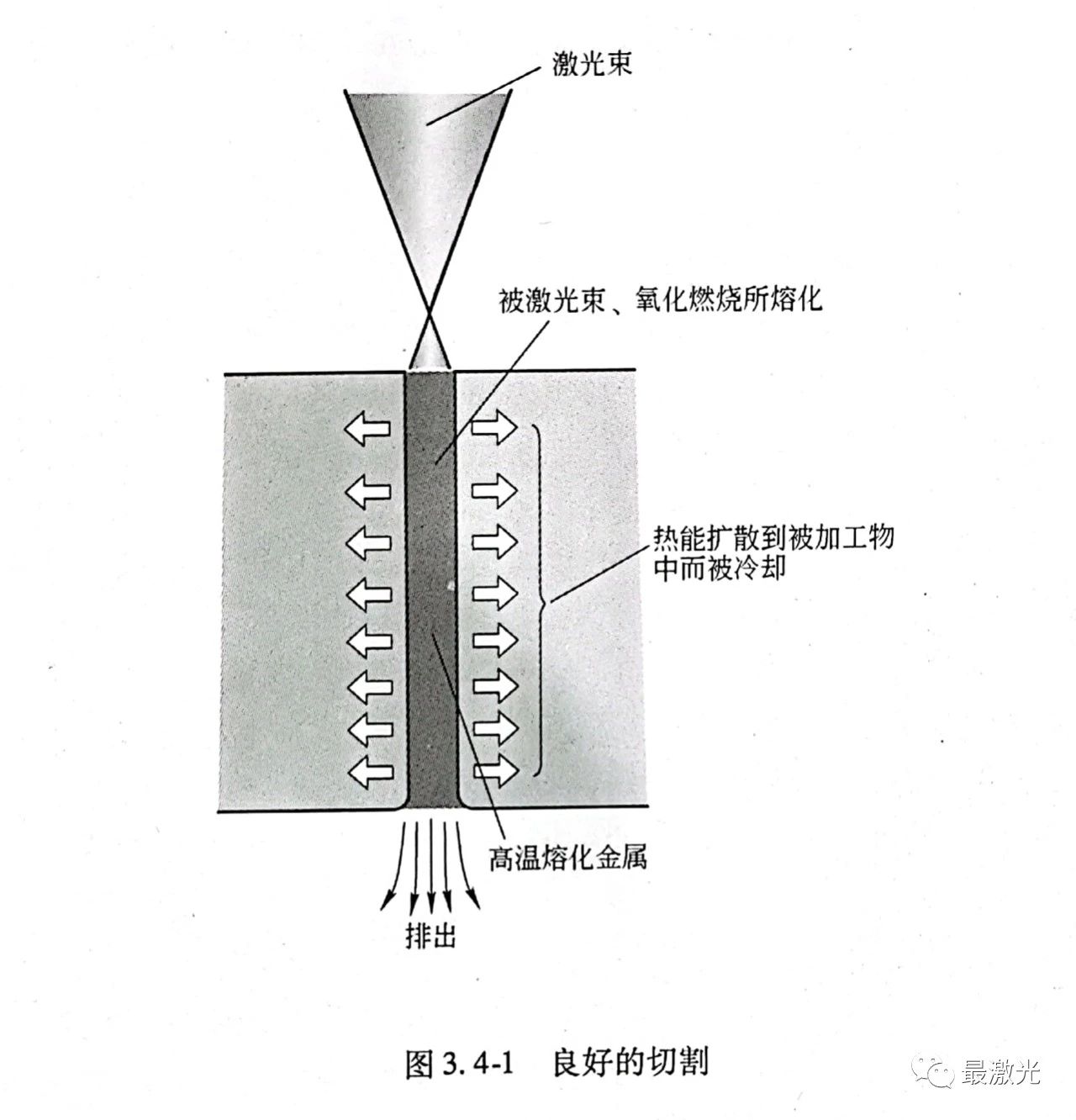
良好的切割如图3.4-1所示,激光照射所产生的热能及因氧化燃烧而产生的热能都被有效扩散到加工材料中,加工材料又能得到有效的冷却。如果冷却得不充分,就会发生过烧。当加工形状中存在尖角时,尖角部分体积较小一侧的散热面积也比较窄小,温度容易上升,极易引起过烧。另外,在穿孔时,由于孔内壁也吸收激光,温度不断在极小的空间内急剧上升,也是很容易发生过烧的。
【解决方法】
(1)进行多个小尺寸形状的加工时,热量将会随着加工的进展而不断积蓄,加工到后半部分时很容易发生过烧。
图片
解决方法如图3.4-2所示,就是要尽量让加工路线分散开来,避免在一个方向上持续,从而使热量能得到有效的扩散。加工路线需要根据实际加工形状进行优化。
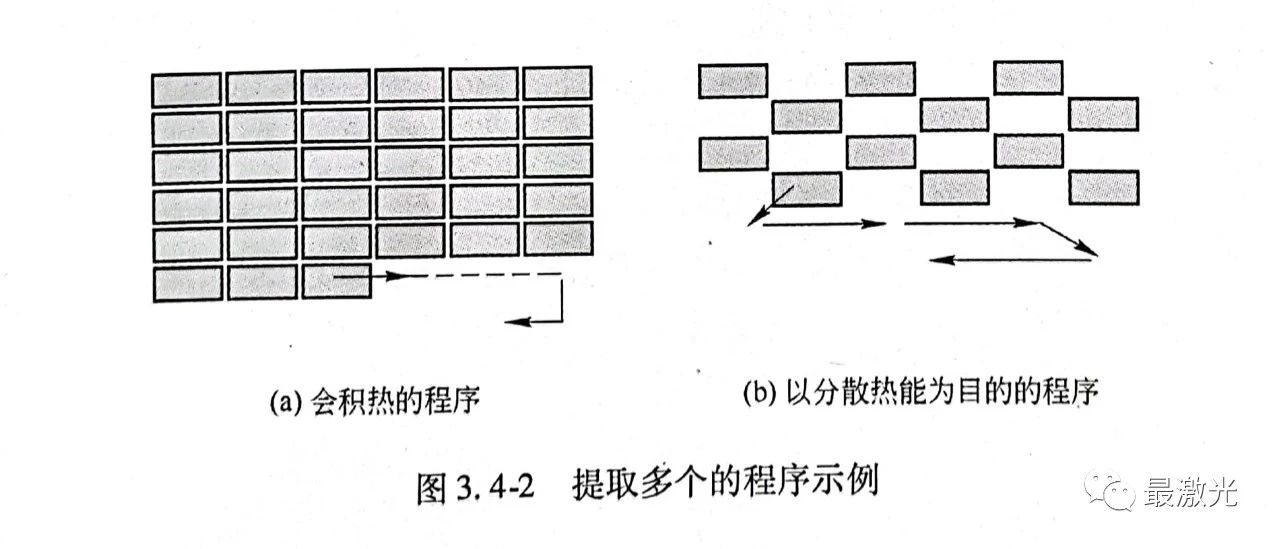
(2)如图3.4-3所示,如果过烧集中发生于尖角部,则可以通过把加工形状中的尖角部改为小圆角R,来有效防止热能的集中。R的数值越大,防止作用就会越有效。加工板厚增加,R值也需要相应加大。
(3)尖角部之所以会随着加工中温度的上升而出现熔损,是因为当激光束通过加工部位时,加工部位已处高温所致(如图3.4-4所示)。
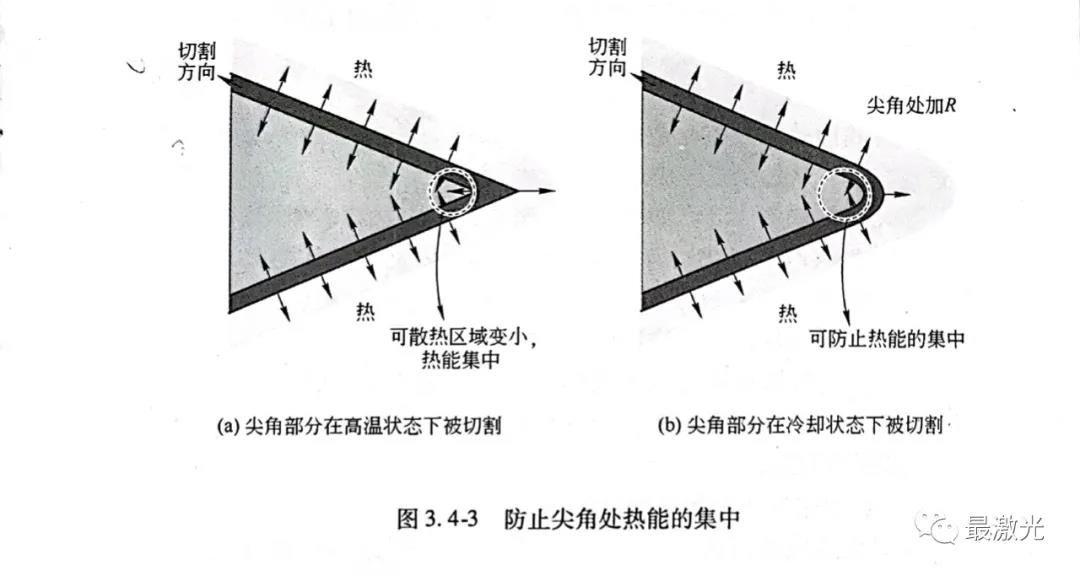
如果激光束的前进速度快于热传导速度,则切割加工就可以在材料还未被加热时完成,可有效防止熔损的发生。9mm厚以上碳钢材料要获得同样的效果,就要使用输出功率在4kW
以上的加工条件,需要使用高输出功率的激光器。
(4)如果辅助气体使用氮气或空气,则不会产生氧化燃烧反应,
基本上也不会发生熔损或过烧。
16毫米厚板产生过烧的原因:被加工物
【现象】
在查找因热能失控而造成过烧的原因时,需要把加工现象按工序进行分解,从每个工序中来查找原因所在。
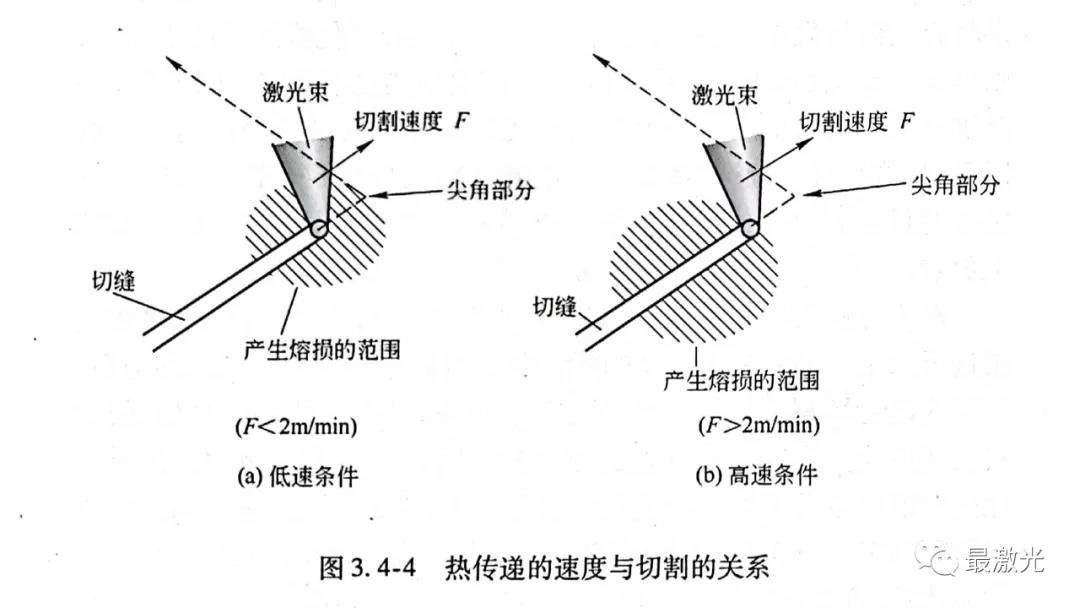
激光切割现象的流程如图3.5-1所示:①向材料表面照射激光;②激光被吸收产生熔化;③产生熔化的部分因辅助气体的助燃而燃烧;④燃烧进一步向板厚方向扩大;⑤熔融金属被从切缝中排出。这些过程不断反复,最终达到切割目的。
过烧产生的原因来自加工机时,将会表现在①、③工序;来自被加工物时,将会表现在②、④、⑤工序。
【原因与对策】
A 原因来自于对激光的吸收时
此时会造成激光切割工序②的不稳定,并因此而导致过烧。如果材料表面氧化皮(黑皮)的紧贴性不好,或氧化膜的厚度不均匀,则材料对激光的吸收就会不均匀,所产生的热也不稳定。
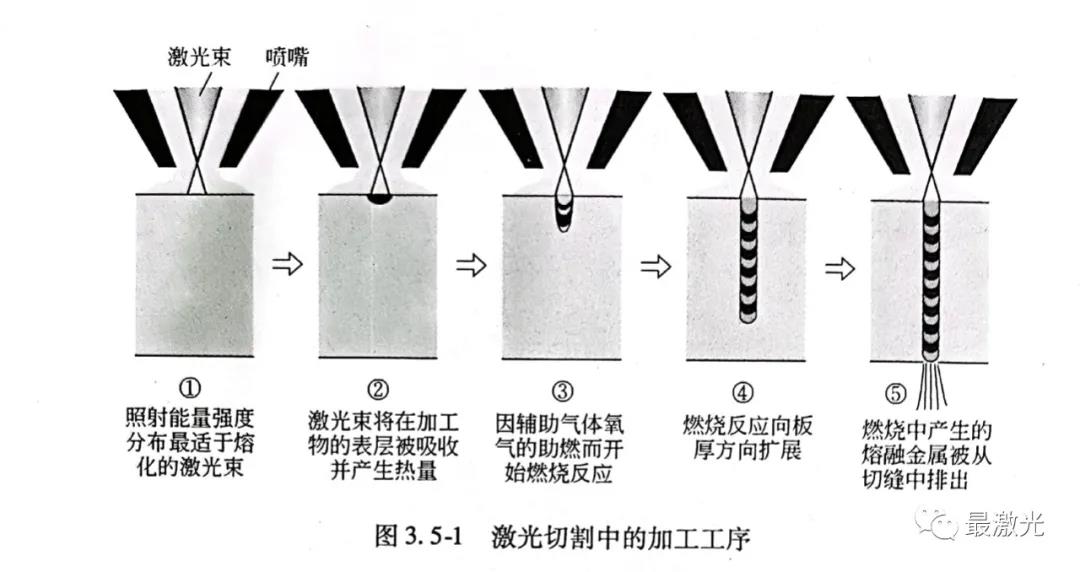
图3.5-2是分别对同一材料的上、下面照射激光进行加工时的切割面对比,可以看出材料表面氧化皮的状况影响着切割面质量。放置材料时,一定要对材料的表面状况仔细进行查看,要把氧化皮状态好的一面朝上放置。
对于那些正反面不能任意进行设置的板材,可以采用二次切割法进行加工。即先利用激光的能量把不均匀的材料表面加工均匀后,再正式进行切割。具体就是:先将激光的能量密度降低到仅能使材料表面熔化的程度,沿着切割形状的轨迹将材料表面熔化,此时熔化的宽度要略大于切缝的宽度。接下来再将条件切换为切割条件进行切割加工。
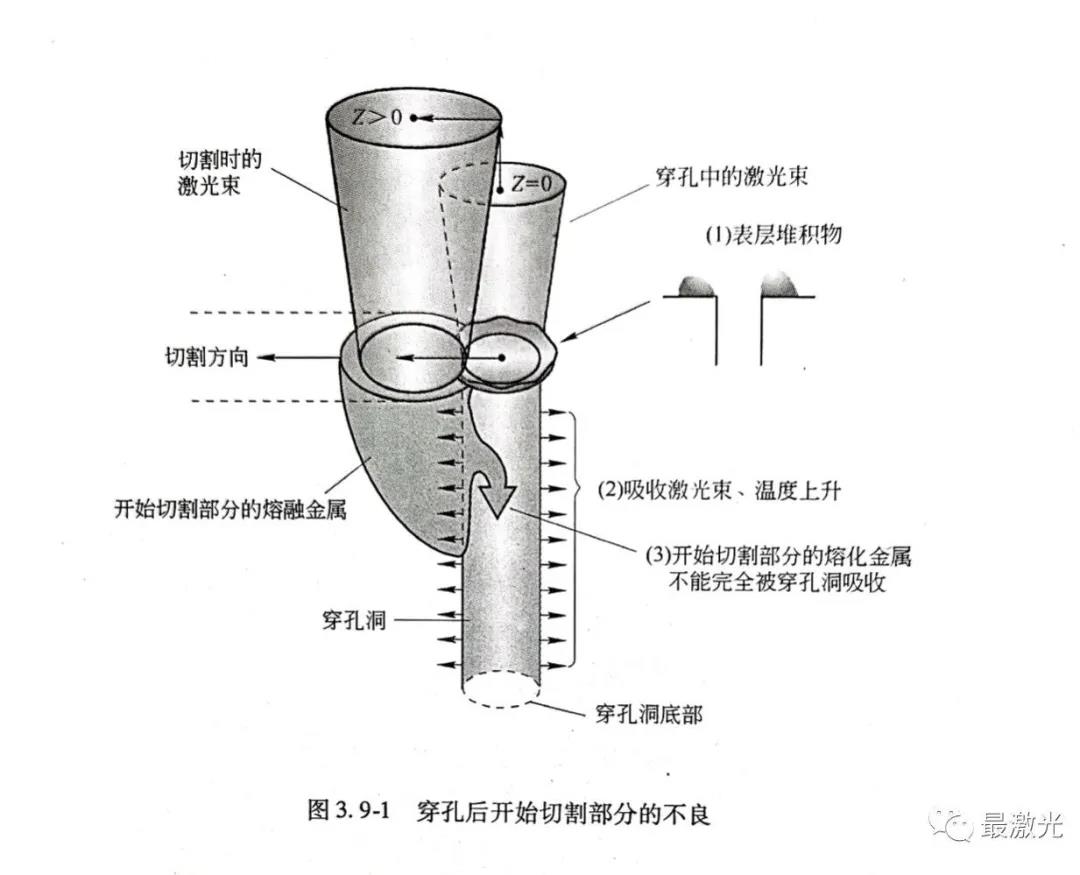
图3.5-3是分别以一次切割法和二次切割法进行切割的样品比较。可以看出,二次切割法切割出的切割面质量基本与表面状况良好材料的切割面质量没有差别。
B 原因来自于向板厚方向的燃烧或熔融金属的排出时
该原因是导致激光切割中工序④和⑤不稳定的因素。
如果材料的内含成分不同,则燃烧反应热的作用或熔融金属的流动状态都将产生变化。日本国内厂家制造的材料在加工性能上没有太大的差别,但海外厂家的材料则在加工性能上差别比较大。
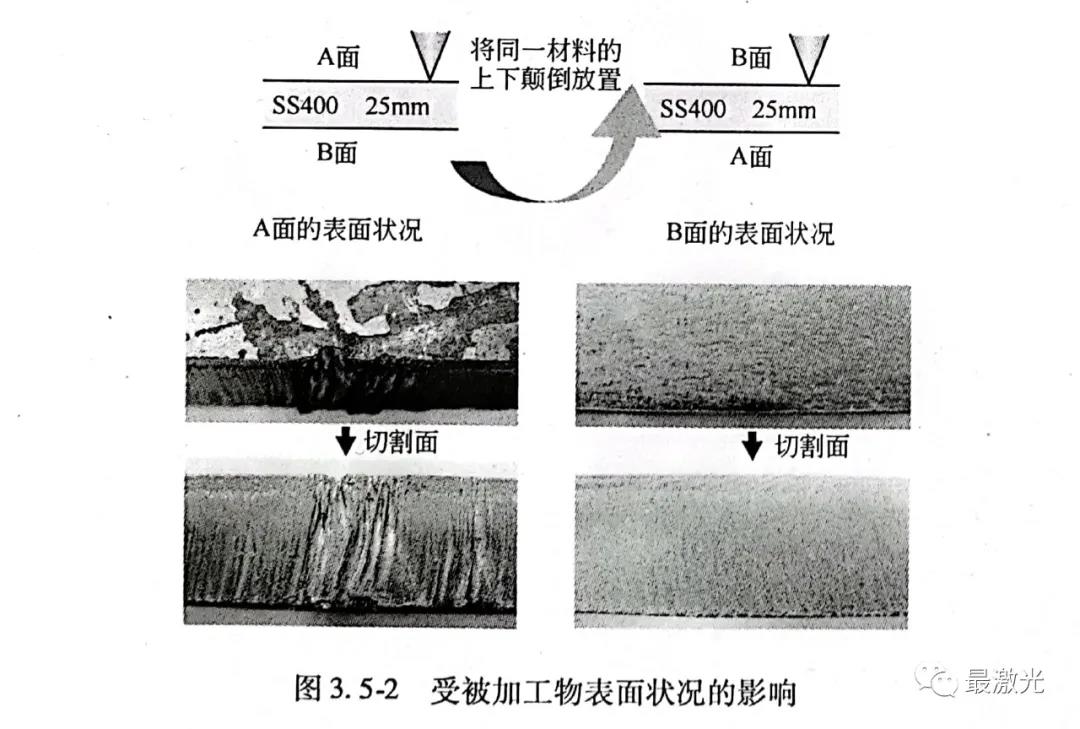
图3.5-4所示为用同一输出功率和切割速度条件对16mm 厚碳钢材料进行切割的对比。如果使用的是含Si或Mn较多的日本国外厂家的材料,则需要在设定条件时特别注意焦点位置及辅助气体压力的设定。
16毫米厚板产生过烧的原因:设备原因
【原因与对策】
A 辅助气体原因(图3.6-1)
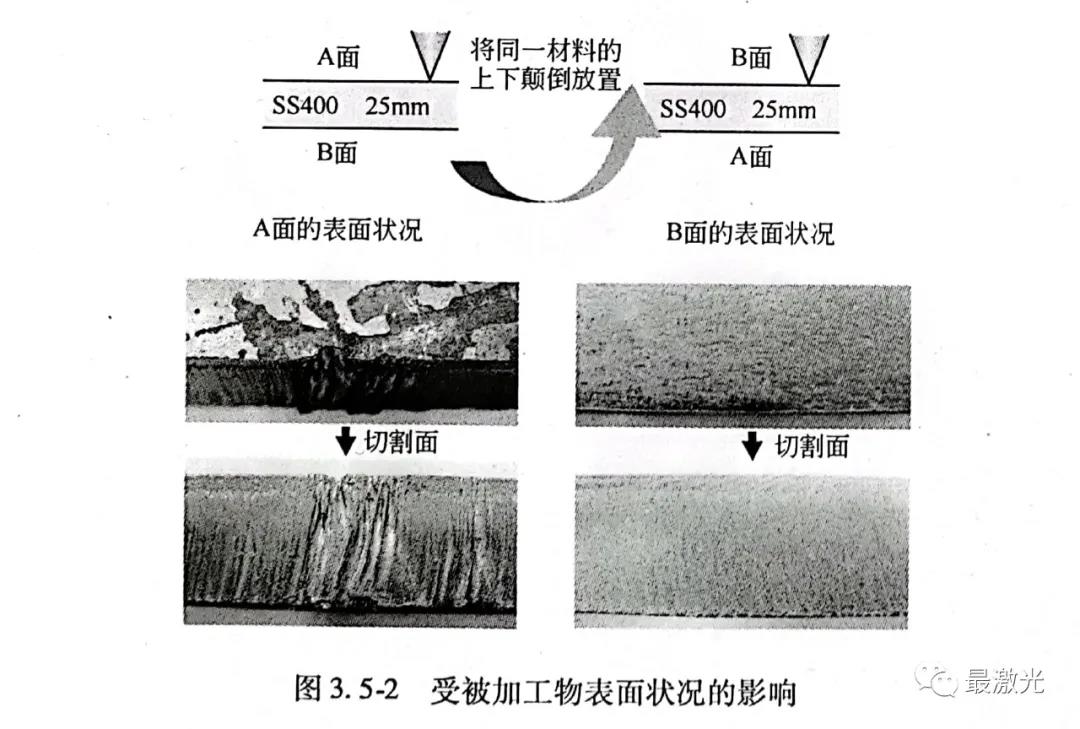
(1)如果氧气没有均匀地喷射到熔融金属的周围,则燃烧能力、熔融金属的流动都会不均衡,极易因不同的切割方向而发生过烧。激光的偏孔,喷嘴出口处的变形、挂渣等,都会造成辅助气流的紊乱,首先需要检查喷嘴状况。
(2)所有的切割面质量都不好时,则可能是因氧气罐中的气体纯度低而致,此时切割面的下部会变粗糙并挂渣。板材越厚,加工质量就越容易受辅助气体纯度影响。查找原因时,应使用曾经实际确认无误的气罐。
B 激光原因(图3.6-2)
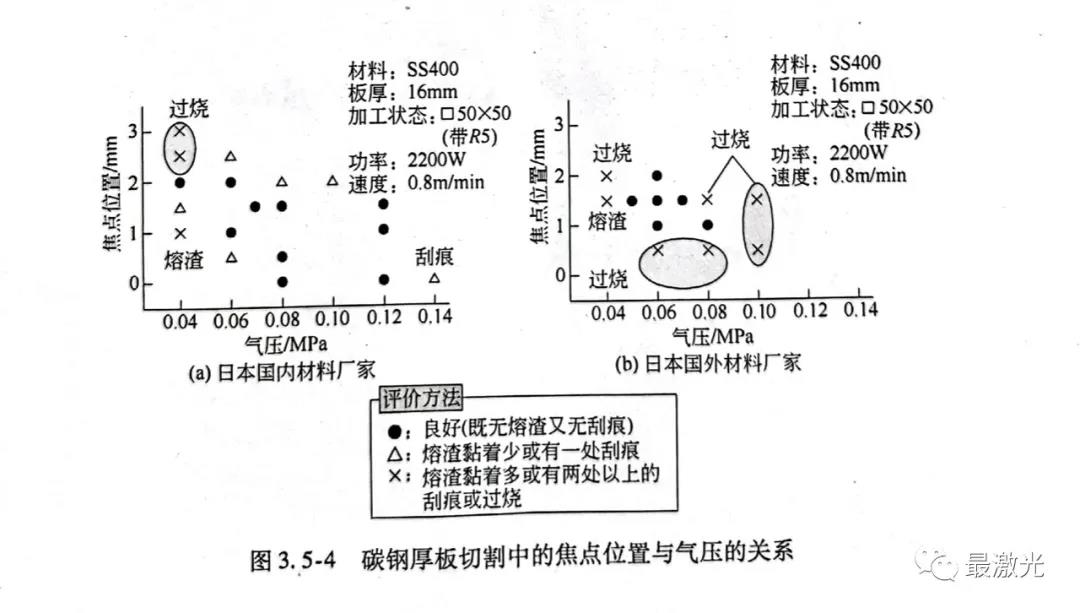
(1)当切割中出现方向性时,很可能就是激光束的圆整度或强度分布存在问题。激光的强度会直接转化为对金属的熔融能力。如果激光束的圆整度或强度分布存在问题,则燃烧能力将会随着切割方向的改变而出现差异,容易造成过烧。此时需要确认光束模式的形状。
(2)当切割面质量全面欠佳时,其原因就在于透镜的聚焦不彻底。需要熔化的地方温度要尽量高,不需熔化的地方温度要尽量低。如果在此温度边界出现高低不明确的能量,就会产生过烧。聚焦不彻底的原因在于透镜、PR镜的异常或光路、折射镜的异常。
C 其他原因(图3.6-3)
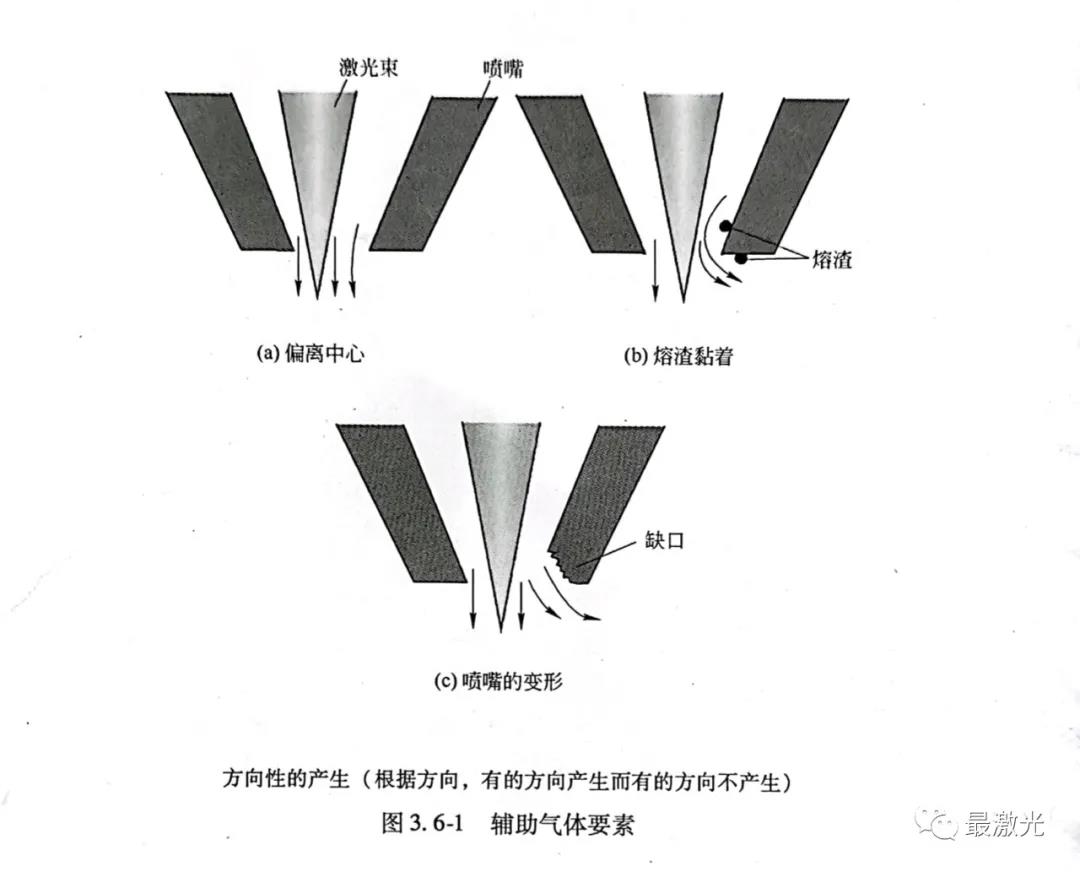
(1)如果加工质量随着加工的进展而逐渐变差,则可能是由于加工中的热量积蓄在材料中,材料温度的上升引起了过烧。此时需要将加工路线设置为热量不会过于集中的分散型路线。
(2)如果质量是从较长加工路线的后半段开始变差,原因就在于透镜或PR镜等的污渍吸收了激光,从而引起了热透镜效应而致。此时需要清洗透镜或PR镜等光学元件。如仍得不到改善,则说明光学元件需要更换了。
(3)如果加工缺陷是产生在加工平台内的某一特定区域,则原因将在于光路出现了偏离。此时喷嘴中心与激光中心会随着加工位置的移动而发生偏离,并因此而导致过烧。此时应对光路进行调整。
22毫米厚板引线过烧的方法
【现象】
在碳钢的厚板切割中,有时会在穿孔过后开始切割的穿孔线(穿孔后的切割初始部分)处出现过烧。而且板材越厚,产生过烧的频率就越高,此时需要把开始切割处设定为开始条件。
【原因】
(1)穿孔过程中所排出的熔融金属会堆积在孔的周围,而当激光经过堆积部时,就会发生激光的反射以及辅助气流的紊乱,从而造成过烧。
(2)在穿孔过程中,因为被加工物的内壁也吸收激光,被加工物的温度会不断升高,很容易导致过烧。如果在孔被穿透之后仍继续照射激光,则被加工物就会被一直加热,温度也会不断升高。
(3)在22mm厚碳钢的加工中,用脉冲条件进行穿孔时,圆孔上口部的直径约为0.4mm,底部约为0.2mm;而切缝上部的宽度则约为0.7mm,下部约为0.5mm.
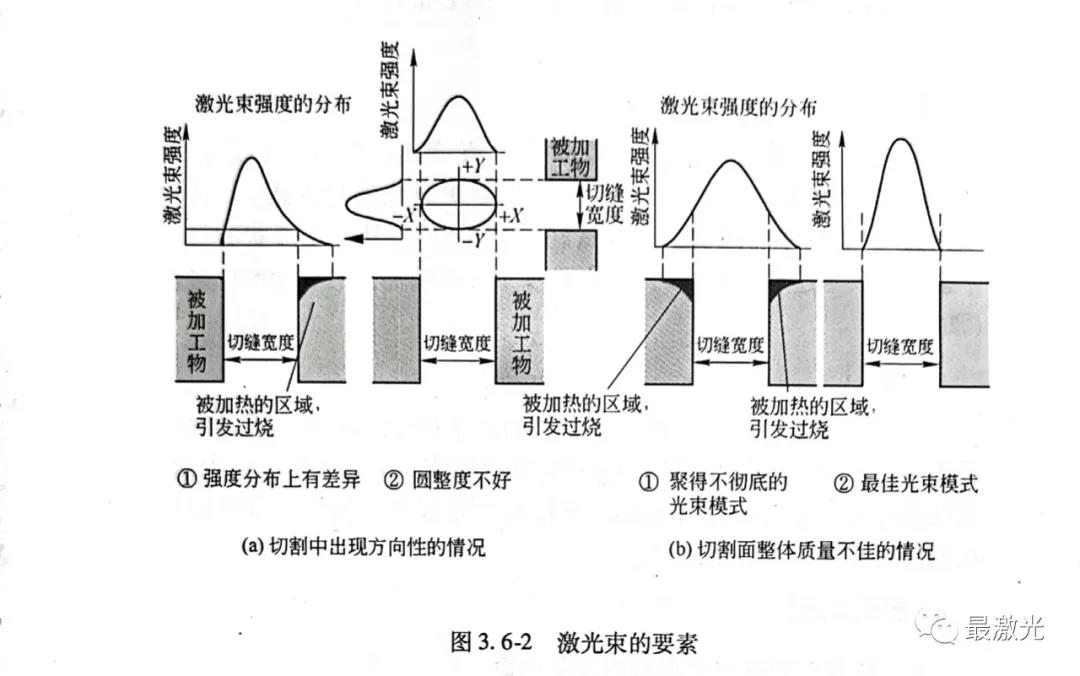
如图3.9-1所示,从穿孔位置开始切割时,圆孔内空间不能将骤然产生的大量熔融金属完全吸收,会形成逆喷造成过烧。
【对策】
A 针对堆积物的对策
解决堆积物的有效方法是:采用单一脉冲能量比较高的低频率、高峰值的脉冲条件,切割时连同堆积物一同切割。虽然使用脉冲条件时速度会比较慢,但熔融与冷却的交错进行,是很适合表面状态不稳定材料的。
B 针对孔壁吸收激光的对策
要避免激光在孔被穿透后的继续照射,可缩短穿孔条件的时间设定,或者通过穿孔传感器来检查孔被穿透的状况并在极短时间内将条件切换为切割条件。
C 针对穿孔直径和切缝宽度不同的对策
将穿孔过后开始切割处所产生的熔融量减少到孔内可以容纳的程度。把切割条件设置为脉冲条件或低速条件就可有效减少熔融量。开始切割处的条件设置是由NC控制装置自动完成的(图3.9-2).
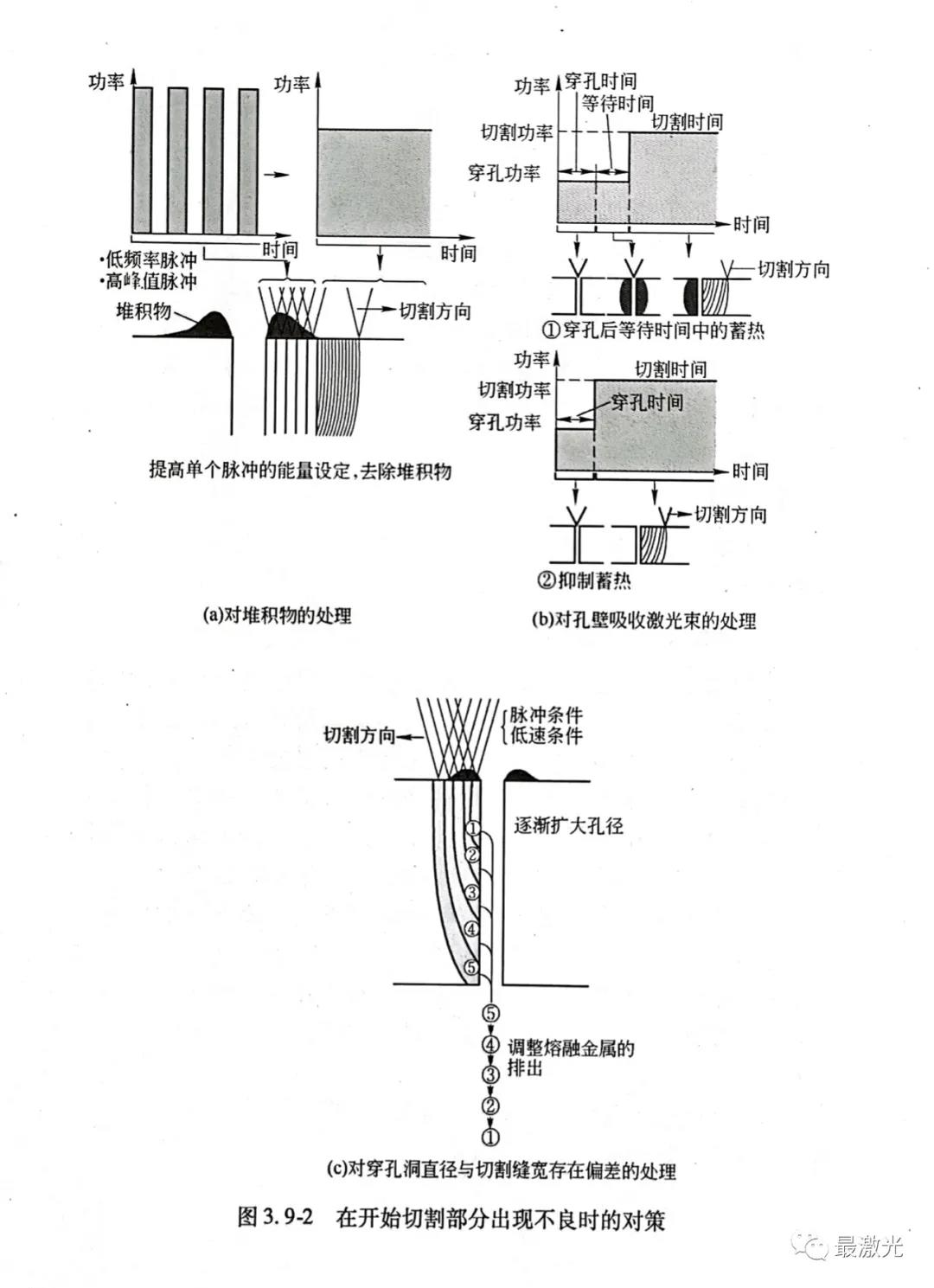